How Your Book Is Printed
how does the book actually get printed and bound to become the beautiful object that sits on your bookshelf?
Before we start our journey, we must give you a brief history of offset lithography printing. First developed in the late eighteenth century, it is based on the principle that oil and water repel one another. An image of the text is transferred photographically onto thin metal, paper, or plastic printing plates. Rollers then apply oil-based ink and water to plates. Since oil and water don’t mix, the oil-based ink won’t stick to the non-image areas of the plate which are water receptive. Only the inked image portion of the plate is then transferred to a rubber blanket cylinder, which transfers the image onto the substrate that is being used.
1. Preparing the plates

Before printing can take place, metal printing plates of the book must be prepared. Rubber is burnt onto each plate, leaving behind a text image of the book.
Originally, the text was made up of individual pieces of metal type assembled page-by-page, rather than being lasered onto a plate digitally – an immensely skilled and painstaking process. Advances in printing technology to what we have today have enabled the production of affordable and mass market books and revolutionised the dissemination of knowledge and art.
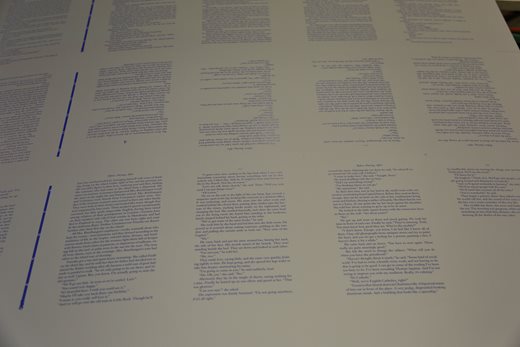
Every printing press has its own specifications that determine how many pages can be produced on a single plate: it’s usually sixteen, but it can be eight, thirty-two, etc. The number of pages must be a multiple of this figure, which is why you’ll sometimes see blank pages at the beginning or end of books. A 1000 page book, for example, can be broken down into sixty-three sixteen page sections with eight blank pages.
2. Printing the book
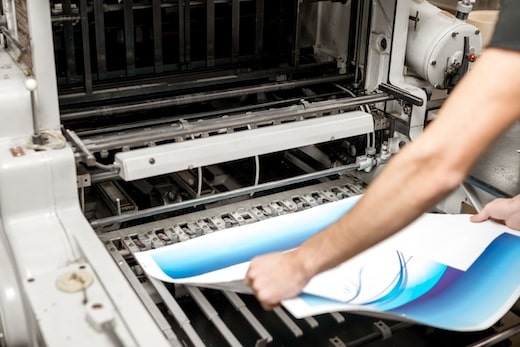
With plates prepared, it’s time for the printing press to work its magic. Depending on factors such as printing volume and production requirements, either a sheet-fed digital printer or an offset machine will be used.
In the sheet-fed process, individual sheets of paper are fed into the printer, while in offset printing, the paper is fed from a roll and passes through the press in continuous motion. Paper sheets enter the print units, passing through the inking system, the damping system and the print cylinders.
First, the rollers in the inking system transfer ink onto the metal plate. Then the rollers in the damping system spray water onto the plate removing all excess ink from areas that do not need ink. Finally, the print cylinders transfer the inked image area onto a cylinder which then pastes the image onto the paper reel.
Both our digital and offset methods offer high-quality results, with offset printing excelling in large-scale production runs and digital printing providing flexibility for smaller batches and on-demand printing.
3. Folding
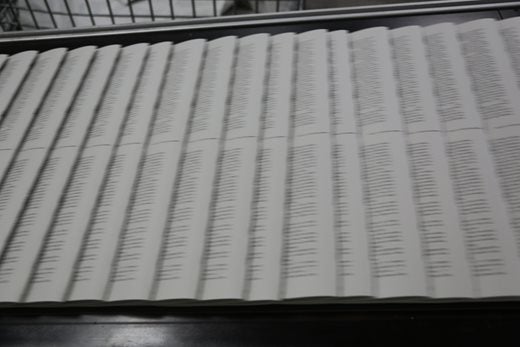
Amidst the flurry of printing, folding quietly takes center stage. Sheets of paper are meticulously folded with precision and care, transforming flat pages into signatures—the building blocks of the book. Each fold is calculated, ensuring proper alignment and consistency throughout the printing process. Whether a simple half-fold or a complex accordion fold, this step is instrumental in preparing the pages for binding and ultimately, the reader’s hands.
4. Preparing the book cover
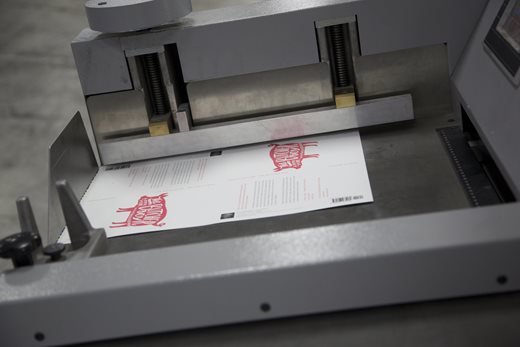
While the pages of the book come to life on the printing press, attention turns to crafting the perfect cover. The cover design, often a visual representation of the book’s content and theme, undergoes its own process of preparation.
The book covers are printed at a separate printer as they require specialized printing – that might be coloured foil or embossing, for example.
Two book covers are usually printed on one sheet of paper. They are cut down to size and trimmed.
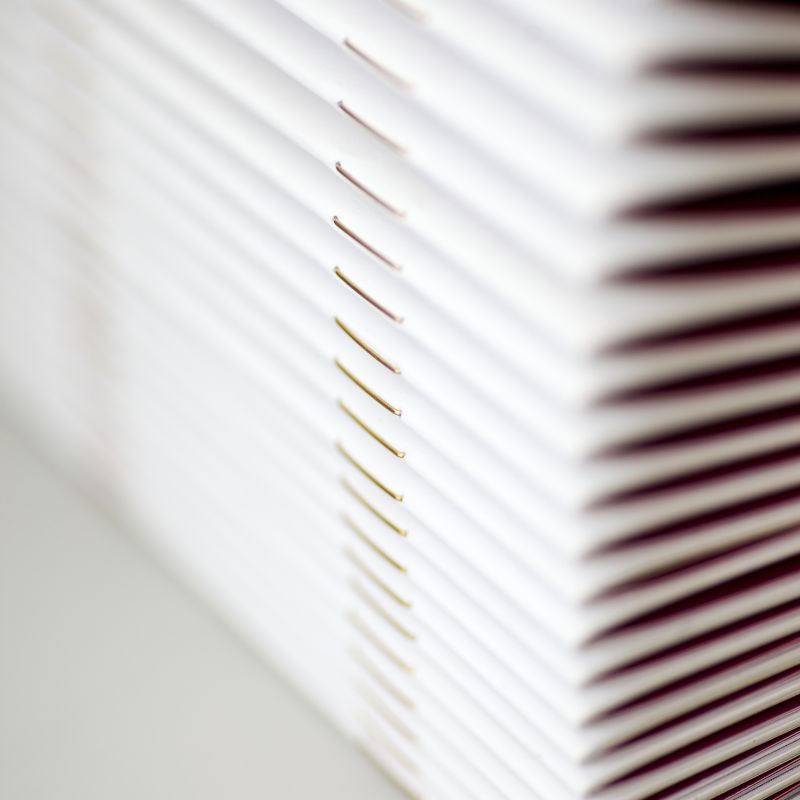
For hardback jackets, cardboard and endpapers are pasted to the covers before the jacket is added to the book.
5. Adding the cover to the book
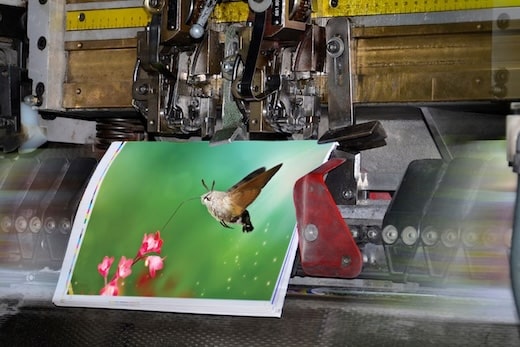
With both pages and cover prepared, it’s time for the final assembly. Depending on the desired finish and functionality, two common binding methods come into play: saddle stitch and perfect bind. In saddle stitching, folded sheets are stapled together along the spine, creating a secure yet cost-effective binding commonly seen in magazines and booklets. Conversely, perfect binding involves gluing the pages to the spine of the cover, resulting in a sleek and professional finish often found in paperback books and catalogs. Each binding method offers its own advantages, catering to the unique needs and preferences of the book’s intended audience.
6. The book!
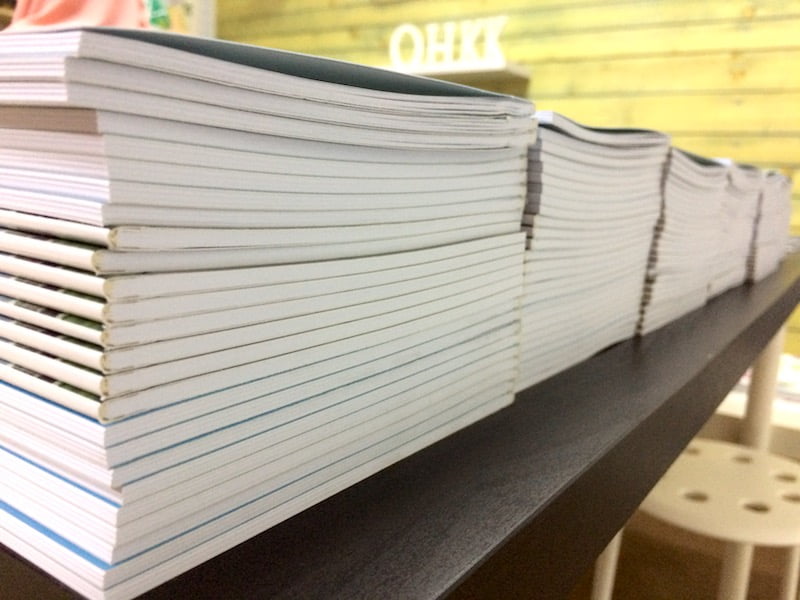
After meticulous preparation and precise execution, the culmination of the printing process is the birth of the book itself. From the crisp pages within to the captivating cover that beckons readers, each element comes together to form a cohesive and immersive reading experience. Whether held in hand or displayed on a shelf, the printed book stands as a testament to the artistry, craftsmanship, and collaborative effort that went into its creation—a timeless masterpiece ready to be cherished by readers for generations to come.